Underground Fiberglass Box Specifications
Why Fiberglass Box Pads Are More Than A Generic Product
Fiberglass box pads are widely used products that many utility companies mistakenly regard as generic. Because price-driven markets force many manufacturers to reduce costs wherever possible, it is common for some to produce only marginally acceptable box pads, resulting in costly “forced” replacement of these inferior products after only a few years of service.
These manufacturers cut costs by using male molds, low quality fillers and simplistic mold designs. Gel coats are eliminated, or the cheapest ingredients are used. Gel-coated products have 10 times the abrasion resistance of non-gel-coated parts. Some companies use straight resin with UV inhibitors to cut costs, but these are much less abrasion-resistant to garden tools, etc. Highly filled resin and low glass reinforcement are the industry norm.
Certain fillers can dramatically affect the life of fiberglass products. Merchandise produced using so-called “chopper-guns” are highly susceptible to inconsistent laminate thickness, due to operator error. More expensive woven “roving fabric” is seldom used by many companies, resulting in poor glass reinforcement. Similarly, encapsulated wood used for support by some box manufacturers often hastens degradation of the vault and resultant failure.
ProGlass products, by contrast, are made with High Quality materials and are the most durable boxes available in the industry. Our boxes are built using highly sophisticated mold designs with built-in intricate ribbing that extends into a wide supporting flange. We begin with an ISO-NPG gel coat formulated with UV additives in Munsel Green. An isothalic DCPD resin, filled with 43% ratio of calcium sulfate flame retardant filler that has successfully passed the UL E-84 and UL E-162 flame and smoke tests.
Calcium carbonate often is used as filler by low-end manufacturers, which is nothing more than fine sand. This filler adds nothing to the flame retarding ability of the resin and results in faster degradation of the composite. All “budget” fillers reduce the design life of fiberglass because of their increased water absorption. This creates a gradual softening and loss of hardness, again resulting in premature structural decomposition and vulnerability.
There are two basic types of glass reinforcement—chopped strand mat and woven products. ProGlass uses an initial layer of chopped fiberglass strands and filled resin in a gel-coated female mold. Continuous strand roving combined with catalyzed resin are fed through a chopper gun and sprayed onto the mold surface. The surface then is rolled to remove air bubbles to create a smooth and attractive exterior finish in which the porosity of the exterior gel coat is greatly reduced and abrasion resistance is increased. Additional materials are applied for the second, third, and final layers.
ProGlass carefully applies the second and fourth layers of woven roving continuous glass fiber strands, bonding them together to form a heavy laminate. Our woven roving weighs 24 ounces per square yard and is of unparalleled quality.
Alternating layers of woven roving and chopped strand mat are used in the structural portion of laminates. This woven roving adds integrity and strength to the finished laminate. Glass content percentage is dramatically increased and consistent laminate thickness is assured. Certain stress areas are reinforced with woven material, and in some cases, structural foam beams are added. The result is a superior product designed with value-added engineering using the highest quality raw materials and constructed to endure extreme conditions. Certified laminate thickness and glass reinforcement content result in a finished product with a long design life and maximum durability.
- PO Box 280 Shelton, WA 98584
- 1-253-884-4008
- sales@proglassinc.com

We're here to answer your questions.
We have trench cover specialists and CAD experts on staff to assist you. We are available to review your drawings and recommend products in an easy-to-review quote. Thank you for choosing ProGlass, Inc. We appreciate your business.
Why choose us
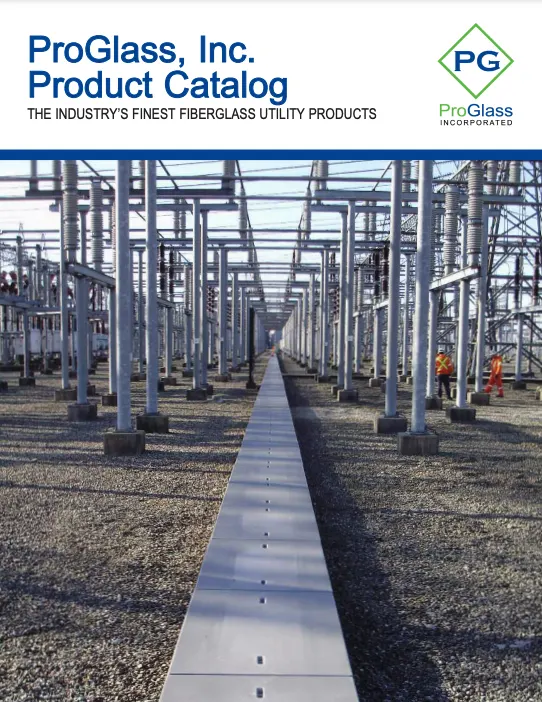
Durable & Long Lasting
Our products are constructed to endure extreme weather conditions (-70˚F to 212˚F). Our C-Type fiberglass and resin mix provide excellent resistance to corrosive elements in the surrounding grade.
Attractive Female Molds
Each product offers a smooth exterior finish that is more attractive and non-porous. Trench covers offer a non-skid, diamond-patterned traction surface for pedestrians or vehicles (H-20 ratings available upon request).
Superior Strength
We use the highest glass reinforcement content in the industry, and incorporate double layers of 24-ounce woven roving reinforcement cloth for ultimate strength.
Lightweight
Our products are easier to handle for a quick installation, so there's no need for bring out the large machinery equipment.
Download The Full Catalog
Customers We Work With
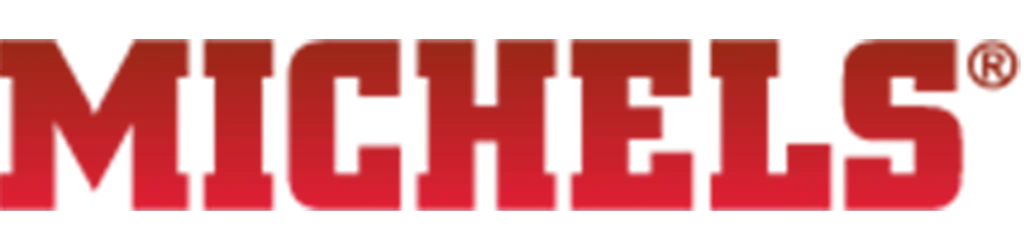
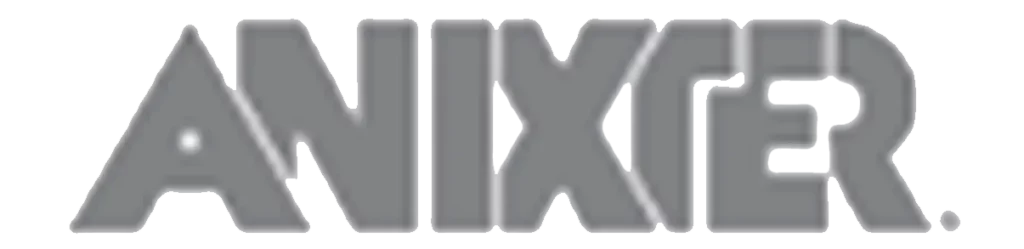
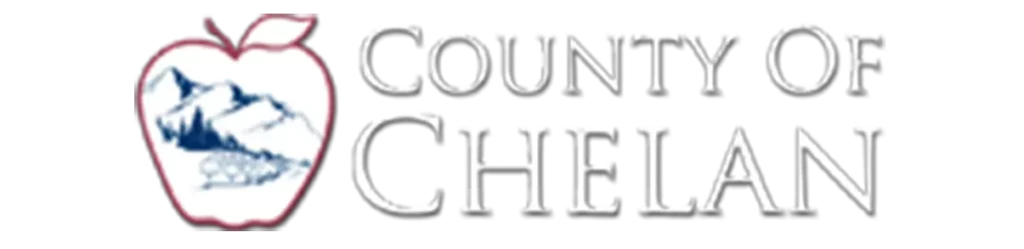
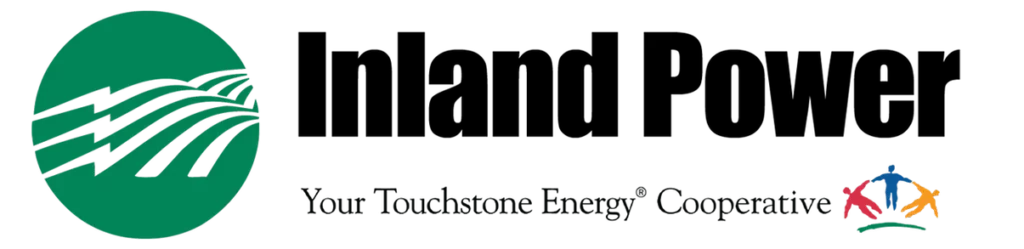
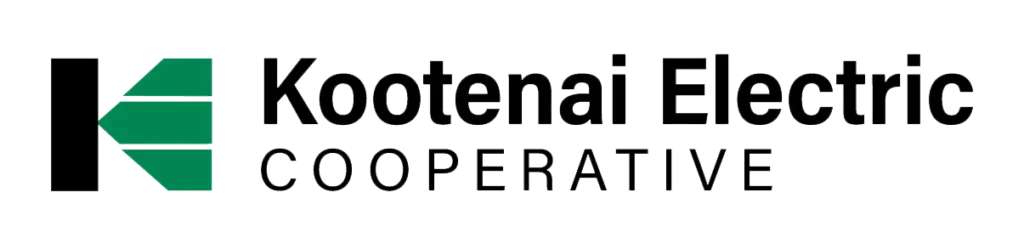
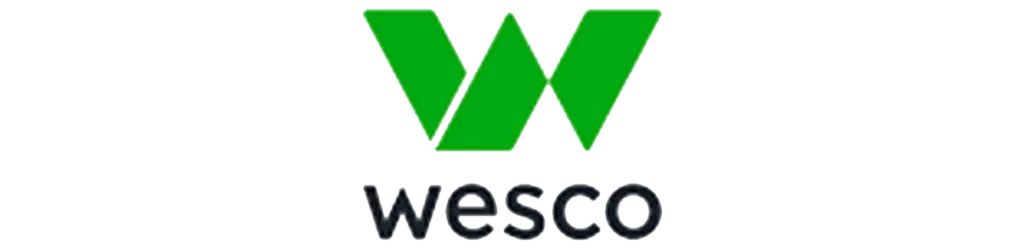
Works Examples
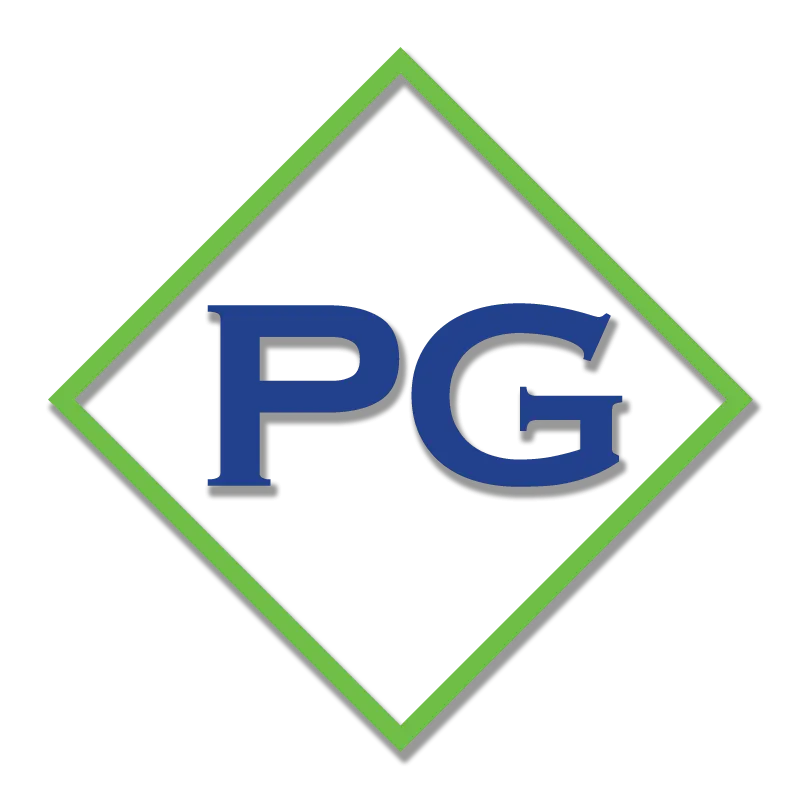